LA CATENA DI TRASMISSIONE

In campo motociclistico la trasmissione a catena è un sistema che offre una elevata sicurezza e un eccellente rendimento, vicino al 97%.
E’ però necessario che vengano rispettate precise regole di scelta, montaggio e manutenzione.
Pochi e semplici accorgimenti consentono di sfruttarne al massimo le potenzialità, riducendo contemporaneamente i tempi d’intervento e garantendo sicurezza, funzionalità e lunga durata.
Al contrario, una non appropriata scelta dei componenti, un montaggio non corretto e una manutenzione non adeguata potrebbero compromettere non solo il comfort di marcia, ma anche la stessa sicurezza del veicolo e del conducente.
In queste pagine, intendo fornire all’utilizzatore alcuni consigli pratici per la scelta, l’installazione, il controllo della trasmissione e la manutenzione di tutti i suoi componenti.
COS’E’ UNA CATENA
Una catena di trasmissione (catena Galle) è composta da una successione di maglie interne e di maglie esterne collegate fra di loro in modo da poter articolare liberamente:
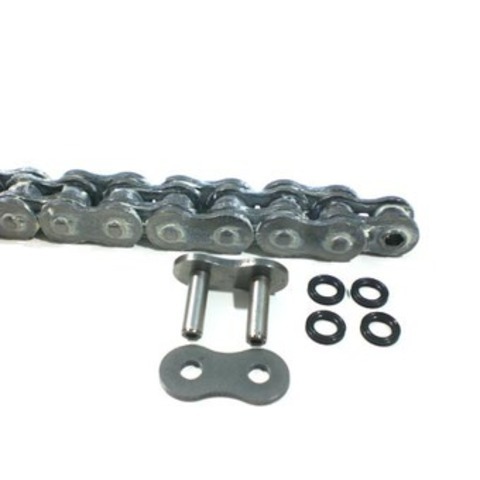
Una catena viene normalmente impiegata chiusa ad anello.
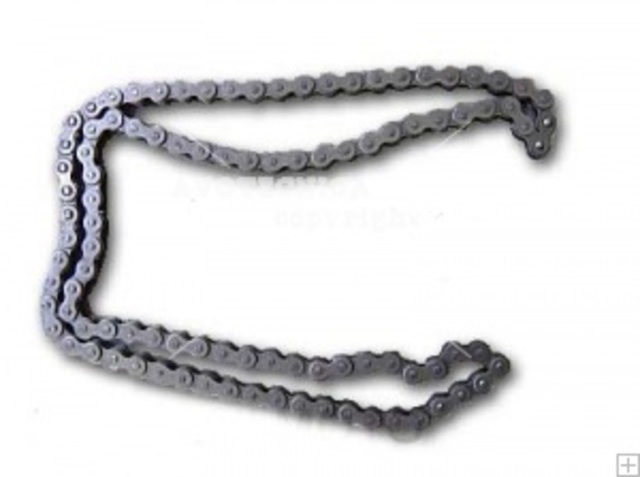
Per collegare fra loro i due capi della catena per formare l’anello chiuso, è necessario impiegare una delle due seguenti maglie di chiusura:
maglia ribadita
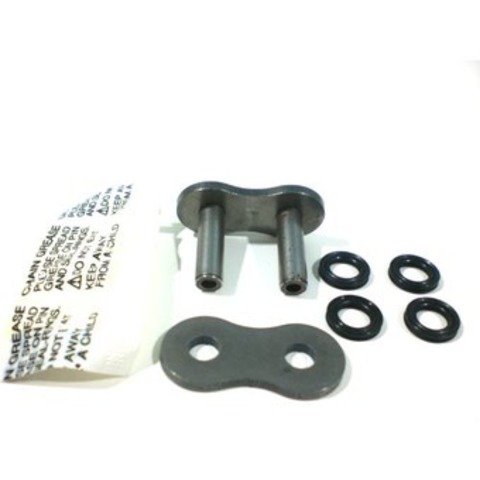
Falsa maglia o maglia a giunto
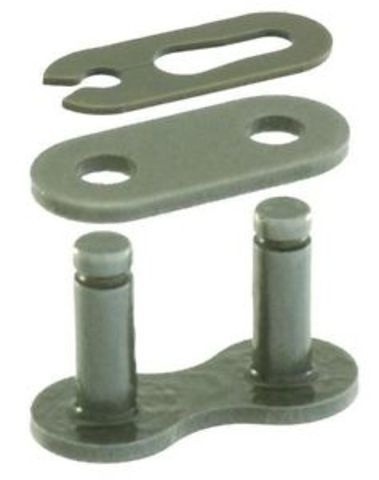
il primo tipo (maglia a ribadire) è la maglia che si usa per chiudere una catena ad X-Ring, perchè essendo una catena pre-lubrificata non c’è bisogno di smontarla per pulirla e/o lubrificarla.
la seconda (falsa maglia o maglia a giunto) si usa sopratutto sulle catene senza O-ring, di solito montata sulle moto da off road, in quanto visto l’uso gravoso e il contatto con terra, fango e polvere, questa catena deve essere smontata, pulita e lubrificata a mezzo immersione nel grasso fuso, quindi è necessario smontarla spesso dalla moto, e quel tipo di chiusura (falsa maglia) rende assai semplice la cosa.
La maglia giunto, anche se è di più facile utilizzo, non può fornire la stessa sicurezza e durata di una maglia a ribadire, per questa ragione si raccomanda di fare il possibile per utilizzare sempre una maglia a ribadire, evitando in ogni caso di utilizzare una maglia giunto per moto di cilindrata superiore a 250 cc.
SCELTA DELLA CATENA
Scegliere la catena più appropriata consultando le info fornite dal produttore della moto, per una corretta selezione in base al tipo, alla cilindrata e all’impiego della moto.
Non modificare il sistema di trasmissione originale, sia nella sua dimensione che nelle sue caratteristiche fondamentali.
CONTROLLO DELLA CATENA
Ispezionare frequentemente la catena, verificando che non presenti articolazioni indurite, o-ring mancanti o danneggiati, altri componenti usurati (con particolare riferimento alla maglia di chiusura).
L’usura della catena può essere facilmente verificata misurando di quanto si è allungata con l’uso.
Si raccomanda di seguire il metodo di verifica seguente che è il più sicuro ed efficiente.
Anzitutto la catena va pulita e rilubrificata, dopo di che si può procedere alla misurazione come segue:
a) porre la catena in tensione se la catena è montata sulla moto, tensionare il ramo superiore inserendo una marcia bassa e ruotando opportunamente la ruota posteriore.
Se la catena è smontata dalla moto, va appoggiata su un piano orizzontale, fissandola ad una estremità e mettendola in tensione tramite un peso di circa 20 Kg applicato all’estremità opposta:
b) con un calibro o con una riga millimetrata di precisione misurare la distanza fra i centri di due perni distanti fra loro di un numero N di maglie (vedere tabella seguente):
PASSO DELLA CATENA
520- 525 – 530 – 532 allungamento massimo ammesso 256,5 mm per tutte le misure elencate in precedenza.
SCELTA, MONTAGGIO E ALLINEAMENTO DELLE RUOTE DENTATE
Verificare frequentemente l’usura dei denti del pignone e della corona, nel profilo e nello spessore: ogni anomalia deve essere rimossa provvedendo alla sostituzione del componente.
ATTENZIONE ! Una catena nuova, se montata su pignoni usurati o danneggiati, si usurerà rapidamente.
Per ottenere le migliori prestazioni, montando una nuova catena occorre montare un nuovo pignone ed una nuova corona, ottenendo così una omogeneità tra tutti gli organi del sistema di trasmissione.
Il pignone e la corona devono essere scelti rispettando le dimensioni di progetto originali.
Per moto stradali di grossa cilindrata sono consigliate corone con denti temprati ad induzione, con ottime caratteristiche di resistenza all’usura.
In fase di montaggio sostituire gli elementi di fissaggio usurati o danneggiati ( viti, rondelle, dadi).
Assicurarsi che pignone e corona, una volta installati, non abbiano sbandieramenti laterali o eccentricità in rotazione.
Controllare l’allineamento tra pignone e corona (che non sempre corrisponde a quello tra la ruota posteriore e quella anteriore)
utilizzando una riga rettificata di lunghezza adeguata o dell’apposito attrezzino facilmente costruibile in garage.
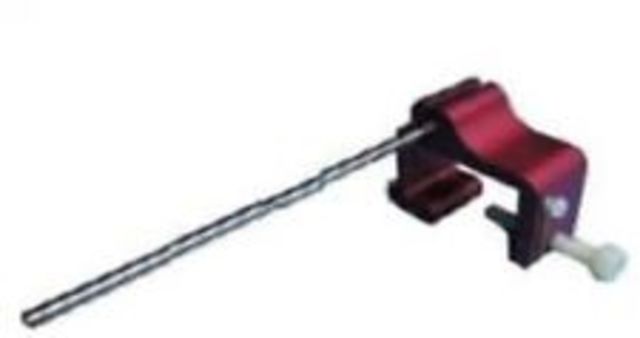
andrà bene anche una corda legata e tenuta a misura per mezzo di un metro.
a) Posizionarla sul fianco esterno della corona, il più possibile vicino al centro di rotazione per garantirsi la più ampia superficie d’appoggio.
b) Verificare che non si evidenzino scostamenti rispetto al fianco
esterno del pignone.
c) Correggere eventuali anomalie intervenendo sui registri di tensionamento della catena o utilizzando degli spessori, senza compromettere il corretto allineamento tra le ruote della moto.
SOSTITUZIONE DI UNA CATENA CHIUSA CON MAGLIA GIUNTO.
Indossare sempre guanti e occhiali protettivi, prestare particolare attenzione alle dita in ogni fase di manipolazione della catena sulla moto.
Sistemare la moto con la ruota posteriore sollevata da terra e quindi libera di girare.
SMONTAGGIO
Fare ruotare la catena fino a che la maglia giunto si venga a trovare sulla corona.
Con l’ausilio della pinza a becchi sagomati sfilare la molletta dai canalini dei perni, la piastra mobile e la forchetta giunto.
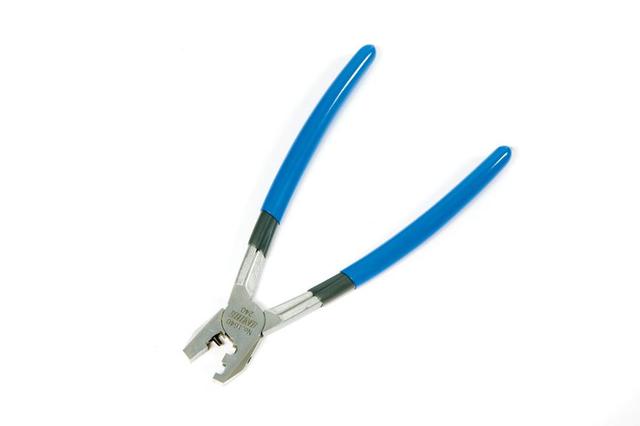
A questo punto la catena risulterà aperta, cioè non più chiusa ad anello.
INSTALLAZIONE
Utilizzando la vecchia forchetta giunto collegare temporaneamente un capo della catena da sostituire con la catena nuova; dopo di che, tirare lentamente l’altro capo della catena vecchia fino a far avvolgere la catena nuova attorno al pignone; proseguire fino a che l’estremità della catena nuova si trovi sulla corona.
Smontare poi la vecchia maglia giunto ed eliminarla unitamente alla catena vecchia.
Avvolgere attorno alla corona anche l’altro capo della nuova catena, in modo che i due capi siano posizionati
l’uno di seguito all’altro su due denti consecutivi.
possiamo ora montarela nuova maglia giunto.
ATTENZIONE !! La maglia giunto è fornita già lubrificata con un prodotto speciale che garantisce una lunga durata: occorre EVITARE ASSOLUTAMENTE di togliere il lubrificante dalla superficie dei perni, perché ciò potrebbe compromettere seriamente la durata della maglia giunto.
In particolare per catene con o-ring, non essendo più possibile una successiva rilubrificazione, questa
cautela è molto importante.
ATTENZIONE ! Le punte della molletta devono essere orientate in senso opposto a quello di rotazione della catena.
ATTENZIONE ! Fare attenzione a non piegare o danneggiare la molletta durante il montaggio.
Verificare che sia perfettamente alloggiata nei canalini dei perni.
Le mollette non dovrebbero essere smontate e montate più di una volta.
ATTENZIONE! Come tutte le parti mobili, la molletta della maglia giunto è sottoposta a continue vibrazioni: controllarne frequentemente lo stato di usura.
ATTENZIONE! Verificare che la catena in esercizio non urti parti metalliche del veicolo, quali carter motore, forcellone, guidacatena o tenditori.
SOSTITUZIONE DI UNA CATENA RIBADITA
Indossa sempre guanti e occhiali protettivi.
prestare particolare attenzione alle dita in ogni fase di manipolazione della catena sulla moto.
Sistemare la moto con la ruota posteriore sollevata da terra e quindi libera di girare.
SMONTAGGIO
Smontare la catena in un punto qualsiasi del suo ramo inferiore, utilizzando lo smontacatene e procedendo
come segue:
a) svitare lo spintore in modo che la punta dello stesso non sia più visibile.
b) svitare la vite di appoggio ed inserire lo smontacatene con lo spintore e la vite di appoggio allineati in corrispondenza del primo perno della maglia esterna da smontare.
c) avvitare lentamente la vite di appoggio 2 sino a che la catena sia bloccata e pronta per l’estrazione del primo dei due perni.
d) avvitare lentamente lo spintore fino a che il primo pernofuoriesca dalla catena per circa metà della sua lunghezza.
e) ripetere le operazioni sul secondo perno e sfilare la forchetta, aprendo così la catena.
oppure usate un frullino e asportate le teste ribattute dei perni.
ATTENZIONE! Quando lo smontacatene universale viene utilizzato per smontare catene con o-ring, è necessario
impiegare l’apposito spessore sagomato (in dotazione) che deve essere inserito sotto la piastra esterna da smontare, a protezione degli o-ring i quali verrebbero altrimenti schiacciati dall’azione dello smontacatene; il mancato inserimento dello spessore causerebbe inoltre il parziale smontaggio delle bussole della catena, danneggiandone la funzionalità e la durata.
MONTAGGIO E CHIUSURA DELLA MAGLIA A RIBADIRE
Utilizzando la forchetta di una vecchia maglia esterna o maglia giunto, collegare temporaneamente un capo della catena da sostituire con la catena nuova; dopo di che, tirare lentamente l’altro capo della catena vecchia fino a far avvolgere la catena nuova attorno al pignone; proseguire fino a che l’estremità della catena nuova si trovi sulla corona.
Smontare poi la vecchia forchetta ed eliminarla unitamente alla catena vecchia.
Avvolgere attorno alla corona anche l’altro capo della nuova catena, in modo che i due capi siano posizionati l’uno di seguito all’altro su due denti consecutivi.
Togliere ora dalla confezione la nuova maglia a ribadire.
a) assicurarsi che sulla forchetta della nuova maglia a ribadire siano montati i due o-ring (uno su ogni perno) appoggiati sulla piastra.
b) inserire la forchetta della nuova maglia a ribadire dalla parte posteriore della catena, evitando ogni contatto con i perni per non asportare il lubrificante.
c) posizionare gli altri due o-ring, uno su ogni bussola.
Girare poi la ruota posteriore in modo che la maglia da ribadire si porti nel ramo inferiore della catena, in una posizione che permetta di operare agevolmente con gli attrezzi.
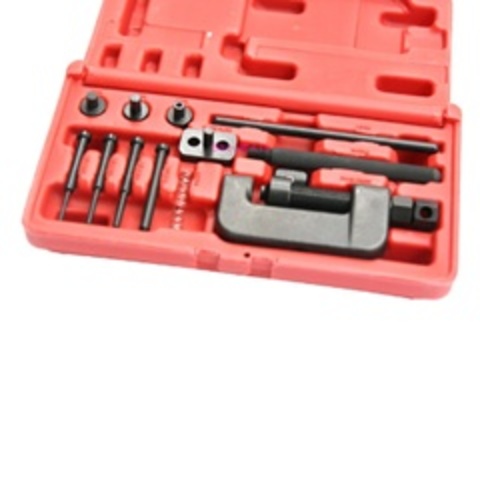
a) collocare la piastra esterna tra le lamelle di tenuta del portapiastra mobile verificandone il corretto alloggiamento.
b) applicare l’attrezzo di assemblaggio sulla catena, inserendo il pernetto di centraggio fra i rulli della catena in corrispondenza con la maglia da ribadire.
c) avvitare con le dita il porta-piastra mobile 1 sino ad imboccare la piastra esterna sui perni della forchetta della maglia a ribadire.
d) con una chiave a cricchetto o con il perno in dotazione avvitate a fondo, ma senza forzare, il porta-piastra mobile inserendo così completamente la piastra della maglia a ribadire sui perni della forchetta.
e) svitare lentamente il porta-piastra mobile liberando la catena.
controllare che i perni precedentemente ribaditi che siano ben chiusi prima di provare la moto.
TENSIONAMENTO DELLA CATENA
Il corretto tensionamento della catena è di estrema importanza per la durata e l’efficienza del sistema di trasmissione posteriore: un eccessivo tensionamento della catena provoca inutilmente dei pericolosi carichi aggiuntivi, che aumentano il carico di lavoro dell’articolazione fra perni e bussole, surriscaldando la catena, consumano precocemente il lubrificante e portano quindi ad una rapida usura della catena; inoltre, se la moto è soggetta a sobbalzi, il movimento alternato a leva del forcellone oscillante può causare alla catena dei contraccolpi violentissimi, che possono portare rapidamente al danneggiamento o alla rottura della catena stessa o degli altri organi ad essa collegati (corona, mozzo posteriore, cuscinetto dell’albero di uscita della trasmissione secondaria ecc.)
Una catena eccessivamente allentata è soggetta a violenti colpi di frusta in accelerazione che moltiplicano il carico applicato alla catena e che possono causare lo scavalcamento delle ruote dentate con seri danni al veicolo e al conducente.
Il controllo e il ripristino della tensione della catena deve essere eseguito con la seguente frequenza:per uso su strada: dopo i primi 100 Km, e, in seguito ogni 400 Km
per uso fuoristrada: dopo ogni utilizzo
PROCEDURA DI TENSIONAMENTO
a) Anzitutto, la catena deve essere posta nella sua condizione di massima tensione .
Questa si ha quando il pignone e la corona sono alla massima distanza.
Per ottenere ciò, occorre caricare la ruota posteriore (fate sedere un amico sulla moto) fino a che i centri del pignone, del perno del forcellone e della corona siano allineati sulla stessa retta .
Il forcellone sarà parallelo al terreno.
b) Agendo sul sistema di tensionamento(registri di regolazione o camme) tendere la catena in modo che il ramo inferiore, preso fra due dita nel suo punto mediano, possa oscillare liberamente dal basso verso l’alto di 10-15 mm (mentre il ramo superiore è teso).
c) Procedere poi al serraggio della ruota posteriore con la catena sotto carico.
Questa condizione si ottiene, dopo aver inserito una marcia bassa a motore spento, semplicemente interponendo un
cacciavite tra catena e corona e girando di pochi gradi la ruota in senso opposto a quello di marcia.
La catena sotto carico consente il corretto posizionamento del perno della ruota, impedendo allo stesso di spostarsi durante il serraggio falsando l’allineamento tra le ruote dentate.
LAVAGGIO
Normalmente l’operazione di lubrificazione della catena è sufficiente per garantire contemporaneamente il lavaggio.
In caso però di eccessivo accumulo di sporco (sabbia, terra, particelle di asfalto e altri residui) intervenire petrolio bianco o lamapante
e procedere immediatamente all’asciugatura della catena con uno straccio pulito
Dopo l’uso fuoristrada asportare fango, terra o sabbia con un getto d’acqua e procedere immediatamente all’asciugatura della catena mediante uno straccio pulito.
ATTENZIONE! Evitare l’uso di vapore o solventi.
Nel caso di pulizia di catene con o-rings, evitare l’uso di spazzole dure o di altri metodi che possano danneggiare gli o-rings.
ATTENZIONE! Subito dopo il lavaggio, la catena va
rilubrificata come descritto più avanti.
LUBRIFICAZIONE
Il ripristino della lubrificazione per catene senza o-ring e la lubrificazione a scopo protettivo per catene con o-ring sono operazioni di grande importanza per la lunga durata e per le migliori prestazioni della catena.
Poichè la funzione del lubrificante è quella di ridurre gli attriti, ne consegue che una carenza di lubrificante ovvero l’impiego di un prodotto non adatto causano un aumento degli attriti specialmente nell’area di lavoro tra perno e bussola delle articolazioni.. Ciò assorbe energia, che si trasforma in calore (con conseguente calo del rendimento della trasmissione) e conduce ad una rapida usura dei componenti metallici.
Inoltre l’aumento di temperatura rende più fluido il lubrificante, che tenderà così a fuoriuscire ancor più
dalla catena, causando un ulteriore aumento degli attriti, e così via.
Di conseguenza, quando si nota che la temperatura della catena in esercizio tende ad essere un po’ elevata, questo è un sintomo di cattiva lubrificazione, per cui occorre procedere al più presto a ripristinare le giuste condizioni di lavoro.
Altri segnali evidenti di cattiva lubrificazione sono un rapido allungamento della catena, la comparsa di zone rossicce (indice di ruggine), la presenza di cigolii e rumorosità della trasmissione.
Per una corretta rilubrificazione della catena procedere secondo le seguenti istruzioni.
LUBRIFICAZIONE DI CATENE CON O-RING
Nelle catene con o-ring la lubrificazione delle articolazioni è assicurata dal lubrificante sigillato dagli o-ring nell’area di lavoro.
Occorre tuttavia provvedere ad una lubrificazione periodica della catena per mantenere morbidi gli o-ring evitando screpolature e conseguenti rotture, e per proteggere dall’ossidazione i componenti metallici della trasmissione.
Utilizzare olio minerale SAE 80-90, o grasso ai saponi di Litio evitando assolutamente l’uso di lubrificanti spray non specifici, che potrebbero. dato il loro contenuto di solventi, danneggiare gli o-ring.
a) stendere su tutta la lunghezza della catena, sia all’interno che all’esterno, un velo di olio con l’ausilio di un pennello pulito.
b) dopo qualche ora eliminare il lubrificante in eccesso utilizzando uno straccio pulito.
ATTENZIONE! Lubrificare la catena ogni 400 Km o più frequentemente se necessario.
ATTENZIONE! Quando possibile lubrificare la catena senza attendere che sia raffreddata dopo l’utilizzo, in modo che il nuovo lubrificante possa divenire più fluido e penetrare meglio nelle articolazioni della catena (nel caso di catene senza o-ring) o essere più efficace nella sua azione protettiva (nel caso di catene con oring)
ATTENZIONE! Non utilizzare la moto immediatamente dopo aver lubrificato la catena, in quanto il lubrificante sarebbe ancora fluido (perché caldo o perché il solvente non è ancora evaporato) e verrebbe quindi subito centrifugato verso l’esterno imbrattando la gomma posteriore e la pedana d’appoggio del conducente.
POTENZIALI PROBLEMI DELLE CATENE DI TRASMISSIONE PER MOTO E LORO CAUSE
ECCESSIVO RUMORE DELLA TRASMISSIONE
errato tensionamento( troppo tesa o troppo lenta)
insufficiente lubrificazione
non corretto allineamento tra pignone e corona
non corretta corrispondenza dimensionale tra la catena e il pignone e la corona
urti o strisciamenti della catena su parti del veicolo in esercizio
usura del pignone o della corona
usura della catena
usura, rottura o disallineamento !di altri componenti della
trasmissione (pattini, guidacatena, tenditori)
VIBRAZIONE DELLA TRASMISSIONE
errato tensionamento della catena (troppo tesa o troppo lenta)
non corretto allineamento tra pignone e corona
presenza di articolazioni indurite
usura non uniforme della catena o del pignone o della corona
LA CATENA SCAVALCA LE RUOTE DENTATE
eccessiva usura del pignone o della corona
eccessivo allungamento della catena causa usura
insufficiente tensionamento della catena
non corretto allineamento tra pignone e corona
non corretto posizionamento di pattini, guidacatena o tenditori
ruote dentate piegate, ondulate, danneggiate o con dimensioni
errate
presenza di corpi estranei tra la catena e le ruote dentate
USURA ALL’INTERNO DELLE PIASTRE DELLA CATENA, PIGNONE USURATO SU UN LATO E CORONA USURATA SUL LATO OPPOSTO
non corretto allineamento tra pignone e corona
INDURIMENTO DELLE ARTICOLAZIONI DELLA CATENA
eccessivo tensionamento della catena
insufficiente lubrificazione
non corretto allineamento tra pignone e corona
ossidazione delle articolazioni della catena
sottodimensionamento della catena rispetto ai carichi cui è sottoposta
rottura o perdita di o-ring
non corretto montaggio ( vale solo per la maglia a ribadire e la maglia giunto)
materiale estraneo (sabbia, fango) nelle articolazioni della catena.
ROTTURA DEI PERNI O DEI RULLI O DELLE BUSSOLE DELLA CATENA
carichi eccessivi o carichi applicati troppo violentemente (caso tipico delle moto prive di parastrappi)
eccessiva usura del pignone o della corona
eccessivo allungamento della catena causa usura
insufficiente lubrificazione
insufficiente tensionamento della catena
non corretto allineamento tra pignone e corona
non corretto posizionamento di pattini, guidacatena o tenditori
non corretto rapporto dimensionale tra la catena, il pignone e la corona
numero di denti del pignone inferiore a quello minimo consigliato (15 denti)
presenza di corpi estranei tra la catena e le ruote dentate
ROTTURA DELLE PIASTRE DELLA CATENA
urti o strisciamenti della catena su parti del veicolo in esercizio
eccessivo tensionamento della catena
presenza di corpi estranei tra la catena e le ruote dentate
forte disallineamento tra pignone e corona
sottodimensionamento della catena rispetto ai carichi cui è
sottoposta
corrosione causata da agenti esterni ( acido batteria, carburante o altri fluidi)
Destroyer